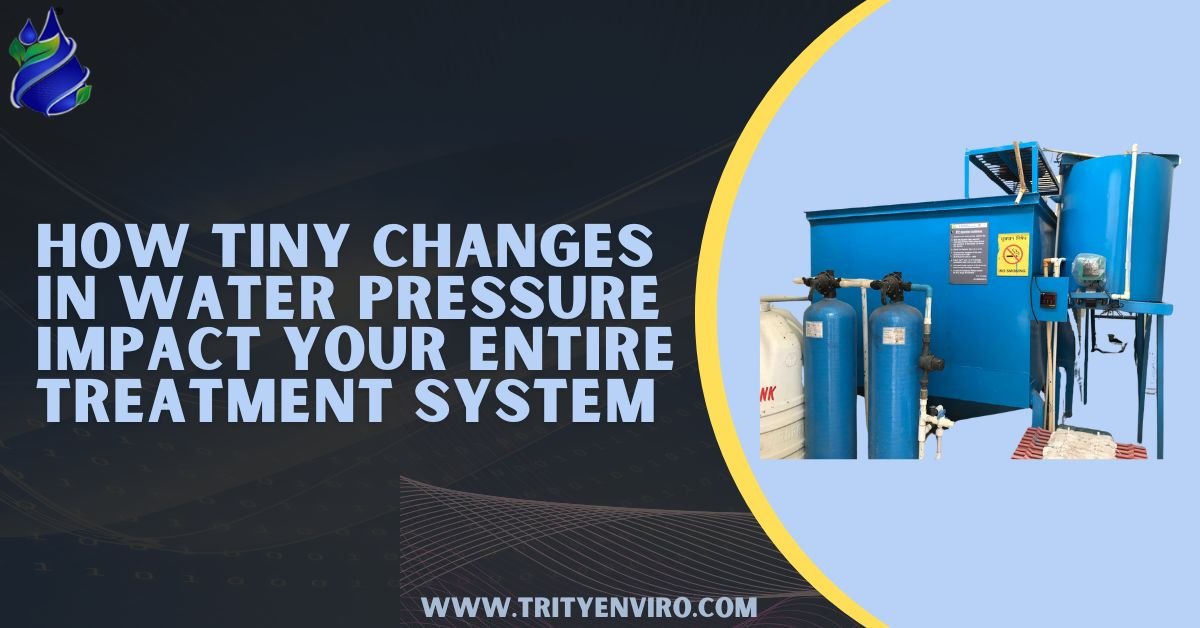
How Tiny Changes in Water Pressure Impact Your Entire Treatment System
Water pressure serves as a generally neglected factor in treatment system management practices. Small variations within pressure measurements can modify both system operation and its energy efficiency and its lifespan. Instabilities of pressure roughen system equipment performance while degrading treatment results and driving up maintenance expenses. Monitoring pressure relationships within a system provides knowledge that prevents system breakdowns. This blog provides details about water pressure effects on treatment systems together with monitoring indicators and proven regulation strategies.
Understanding the Basics: How Water Pressure Affects Treatment Systems
1. The treatment system depends on water pressure as its main driving force for carrying water through pipes alongside pumps, filters, and membranes. An adequate water treatment plant requires steady water pressure because low pressure levels make the system unable to achieve proper water movement, which decreases overall system operation. Systems endure compromised components when pressurization exceeds optimal levels, which simultaneously drives up operating expenses.
2. Reverse osmosis systems function with a necessary pressure to push water across the semi-permeable membrane. At current pressures below the minimum threshold the filtration process becomes slower which leads to poor water production efficiency. Steady pressure maintains filter performance in water treatment plants.
3. Fluctuating pressure can produce two problematic effects which include filter clogging and impurity release those results in inferior water quality. The complete system works efficiently when water pressure stays at the optimum level. The sustained application of pressure enhances operational speed and lowers both operational energy utilization and equipment deterioration rates.
Small Fluctuations, Big Consequences: The Science of Water Pressure Changes
Even nominal pressure changes will generate compounding effects throughout your treatment system. Productivity levels suffer when pressure drops slightly because water becomes disproportionately distributed across filters and membranes. The equipment's filtration quality reduces alongside the occurrence of contaminants entering the system. High pressure peaks generate severe stress to system components such as pumps, seals, and valves. System components gradually show decreasing strength through pressure accumulation, which finally leads to various breakdowns and operational failures. Transmembrane pressure plays a crucial role in maintaining consistent filtration performance, ensuring contaminants are effectively removed.
The flow of water during treatment depends entirely on established pressure differences between system points. System efficiency suffers when operational pressure rises above or falls below its intended threshold values. Pressurized systems experience elevated velocity flows that produce turbulent conditions. The velocity turbulence results from pressure fluctuations, which produces pipe erosion and membrane destruction. Systems under low-pressure conditions maintain slow water flow that enables sediments to accumulate and clog system components. Understanding pressure-induced effects on flow dynamics enables operators to implement actions for pressure regulation, which ensures system performance consistency.
Signs Your Treatment System Suffers from Pressure Inconsistencies
1. Changes in system pressure do not always become visible until the problem manifests. System efficiency and output performance suffer from several potential manifestations of these underlying issues. The most noticeable indicator appears as an abrupt reduction in flow speed. A protracted water transit time through the pipeline indicates that pressure levels are too low.
2. The measurement indicates extra pressure when there is sudden improved flow. You can identify low pressure issues based on the changes in normal pump and pipeline audio frequencies. Listening for sudden gurgling or hissing or banging noises helps identify pressure-related problems. Acoustic disturbances form when water experiences irregular movement because of unequalled pressures. Leaks are another red flag.
3. Pressures beyond normal range lead to valve and seal failures that produce water leaks from the system. High pressure exposure will cause both damaged pipes and membrane cracks. System performance issues signalling excessive pressure include delayed cycles and degraded water quality and repeated equipment shutdowns. Early warning system indicators can help stop major repair work and avoid system downtime.
How Low Water Pressure Impacts System Efficiency and Performance
Treatment systems repeatedly experience low water pressures which generate harmful repercussions throughout the network. Visual evidence shows that system capabilities decrease substantially whenever the pressure reaches levels below standard operating criteria. The efficiency of filtration systems decreases when operating without consistent pressure for achieving proper impurity removal. Low pressure requires less power for filter water movement which leads to incomplete filter processes. Water quality becomes compromised when contaminants manage to pass through systems that operate at low pressure. The operating efficiency of pumps decreases whenever operating pressure remains insufficient.
The system requires additional energy to achieve adequate water movement. The excess stress that builds up will reduce the operational lifespan of the pump. The separation operation during reverse osmosis becomes impaired when system pressure falls below optimal levels. Because pressure is insufficient the system produces less clean water while generating increased wastewater output. The process produces less effective results which drives operational expenses up. Quick identification of low pressure conditions helps avoid equipment problems. A system's optimal pressure performance is assured through regular maintenance monitoring activities.
Preventing Damage: Managing Water Pressure for Optimal Operations
Detecting pressure fluctuations requires ongoing proactive management activities. The routine examination of equipment together with appropriate maintenance activities and pressure control mechanisms represent vital components needed to achieve optimal operations. Pressure gauges together with sensors provide an effective way to monitor pressure regulation. The devices track pressure conditions right away so operators can adjust system parameters. The system uses sensors which activate alarms during conditions when pressure exceeds defined boundaries. Pressure regulation systems work as valuable instrumentation within water and wastewater treatment and industrial operations. These devices achieve consistent pressure through their control of flow rates. These components protect assembly parts such as valves and seals against damaging motion patterns.
System maintenance protocols guarantee equipment runs with maximum operational effectiveness. An effective maintenance program includes both cleaning filters and membrane changes as well as inspecting valves to avoid blockages and prevent leaks and maintain consistent pressure levels. Proper pump maintenance helps prevent damage which occurs when operating pressure rises or falls outside recommended levels. A combination of sophisticated automated pressure control systems delivers the highest level of pressure management. The combination of programmable logic controllers (PLCs) enables these systems to perform automated pressure monitoring and adjustment tasks.
Tools and Techniques to Monitor and Regulate Water Pressure
1. Monitoring together with regulatory control enable the maintenance of optimal water pressure levels. Tools along with specific techniques exist to help operators reach these targets. Pressure gauges function as the backbone for any treatment system. The tools deliver precise measurements of pressure across different system locations. Checking pressure gauges on a regular basis helps operators keep pressures inside allowed limits. Flow meters serve as an important operational measurement solution.
2. Staff utilizers flow meters to monitor water speed which helps track system operational efficiency. Flow rate measurements help identify low pressure conditions through their sudden decline yet noticeable increases signal excessive pressure. By adding sensors to the monitoring system together with alarms operators can get improved visibility to system status. Technology-based sensors identify changes in system parameters and automatically send alerts to machine controllers.
3. Rapid detection of events allows operators to implement immediate corrective measures which stop the damage from intensifying. Automated pressure control systems represent the most effective method to manage system pressures. Advanced technology allows these systems to track pressure levels and perform immediate system adjustments. Such systems eliminate the requirement for worker intervention which conserves time and budget costs.
4. Pressure management best practices need to be followed by operators. Regular facility inspections should happen alongside component cleaning requirements and faulty part exchange protocols. Operators who complete proper training become proficient with monitoring tools because of it.
Conclusion
While water pressure changes might appear innocuous, they actually create major effects on your treatment system. Unstable pressure interrupts flow rates while causing equipment breakdowns and leading to degraded water quality. Knowledge about water pressure effects allows you to adopt preventive actions for achieving continuous system efficiency. Operation of your equipment depends on monitoring tools plus pressure regulators alongside advanced control systems to maintain consistent pressure conditions.
Long-term system reliability depends on scheduled maintenance combined with trained personnel execution. Rapid identification of pressure variations allows you to stop unnecessary costs and operate with better system effectiveness. Water pressure functions as the essential structural element for all treatment systems. Effective resource management improves operational results and lowers costs while delivering superior quality water to recipients.