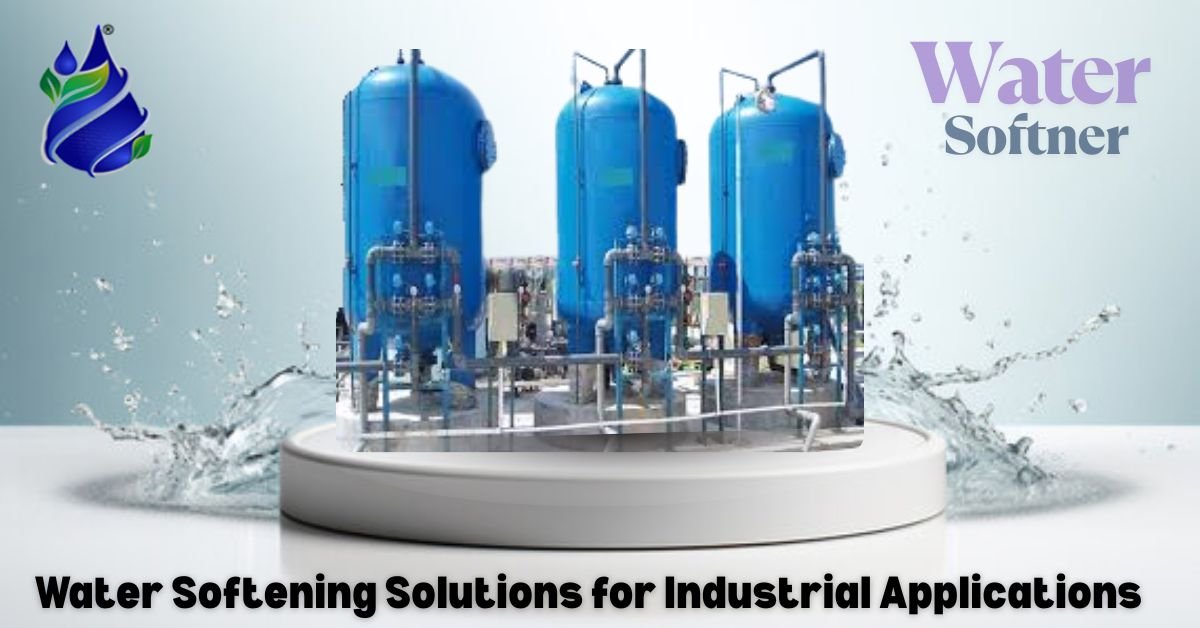
Why Water Softening Is Crucial for Industrial Equipment Performance
Modern industrial facilities have sophisticated machinery for smooth operational running. When water accumulates a high number of minerals, especially calcium and magnesium, it is said to be hard. Scaling, corrosion, and poor operation are effects of hard water. Water softening removes hardness causing minerals. This will also ensure clean water flow while preventing scale deposits of machinery. Softening will not go a long way because internal components may degrade more quickly.
This reduces the life of boilers, cooling towers, and piping systems. A wastewater treatment plant plays a crucial role in managing water quality across industrial processes. Water that is softened increases production efficiency in heating and cooling. It also reduces energy cost due to the maintenance of thermal conductivity at optimal measures. Industrial operations are capable of a continuous operation without any unplanned shutdowns occasioned by equipment failure.
Common Industrial Problems Caused by Hard Water
1. Scale Formation in Boilers and Heat Exchangers- Hard water will deposit scale in the boilers and heat exchangers. Using this insulation reduces heat transfer phenomena while causing loss of energy. As time goes on, overdosages can cause overheating and damage to the structure.
2. Reduced Equipment Efficiency and Increased Downtime- Deposit of minerals in the routes of water passage in machinery. This impacts pressure levels, flow rate, and operations speed. Poor performance causes regular maintenance as well as production delays.
3. Corrosion and Pipe Blockages- The hardness of water minerals are deposited in pipes and corrode these metals. Deteriorated pipes undermine the strength of structure and pose leakage hazards. Blockages burden flow and can cause full shutdowns.
4. Increased Detergent and Chemical Consumption- Hard water combines with cleaning agents and decreases cleaning agent’s performance. More chemicals are used to achieve their results by the industries. This increases the costs and increases waste discharge.
5. Decreased Product Quality in Sensitive Manufacturing Processes- Some of the industries in sectors such as pharmaceuticals and food processing need ultra-pure water. Final products are contaminated with hard water and poses compliance violations. This injures reputation and money is lost as well.
Types of Water Softening Systems Used in Industrial Settings
Different softening technologies are employed by industrial operations based on size and quality of water. These systems are designed for efficient high volumes treatment:
1. Ion Exchange Softeners- These systems utilize dimensional resin beads exchanging hardness ions with sodium or potassium. They have high flow rates and are applicable to continuous processes. Greater ion exchange is suitable for the general manufacturing and HVAC systems.
2. Reverse Osmosis (RO) Systems- RO units pass water into a semipermeable membrane. This eliminates hardness minerals but also salts, bacteria and contaminants. RO systems are an ideal fit in industries that demand ultra-pure water e.g electronics and food processing.
3. Electromagnetic Water Conditioners- These systems change physical properties of mineral ions. They prevent mineral build up on surfaces but do not dissolve mineral deposits. They are normally used as pre-treatment or together with other systems.
4. Lime Softening Systems- These use magnesium and calcium, which precipitates out with the help of calcium hydroxide. They are effective in treating high volumes of water. The municipal and power generation industries are among the most common users of this method.
5. Template Assisted Crystallization (TAC) Systems- TAC – systems convert hardening minerals to harmless microscopic crystals. These do not stick when they get through equipment. They need less maintenance and neither salt nor chemicals.
How Water Softeners Extend the Lifespan of Industrial Equipment
Water softeners shield machineries from damaging from inside. They remove scale build-up which can cause overheating to the boilers. This confines energy consumption to desired limits and releases system strain. Mineral clogging of valves and pumps is also prevented by softeners. Clean water flow deals steady pressure and decreases wear. It enhances the reliability of sensitive equipment in the long term. Water cleaning prevents corrosion in metallic components.
Less corrosion results in fewer leakages and pipe replacements. Softeners also ensure that lubricants operate at optimal levels, through cleaning surfaces and maintaining them smooth. When equipment has its longevity increased, replacements become less frequent. This results in reduced capital outlay. Facilities experience reduced interruptions and twice the consistency in output. A proper sludge treatment process ensures the efficient handling of waste generated during water softening.
Choosing the Right Water Softening Solution for Your Industry
1. Assess Your Water Hardness Level and Volume Needs- First, check the level of calcium and magnesium in your water. Robust systems such as lime softeners or scrubber units may be required because of high flow. Never base sizing system on trough demand.
2. Match the Technology With Industry Requirements- The ultrapure water is required by the pharmaceutical, and food sectors. Reverse osmosis or mixed-bed systems are appropriate for these needs. For heavy industries ion exchange or lime softening is usually sufficient.
3. Evaluate Cost vs. Long-Term ROI- Also consider the system purchase, installation and operation costs. An increased initial investment in effective softeners can minimize energy consumption and maintenance too. This leads to long term savings and better output.
4. Ensure Regulatory Compliance and Environmental Goals- Choose systems that comply with standards for local water discharge. Eco friendly systems such as TAC minimize wastage of chemicals and achieve sustainability objectives.
5. Plan for Maintenance and Support- Select solutions with reduced downtimes and simple servicing. Vendors offering technical support and training in order to optimise system performance.
Cost Benefits of Implementing Water Softening Systems
Water which has been softened reduces energy bills for heating and cooling. Buildings of heat exchangers function more efficiently when not insulated by scale. This results to highly significant energy saving monthly. Maintenance costs also decrease. Technicians use less labour repairing equipment containing mineral deposits. This releases resources to other important plant activities. Equipment failure related production losses are rarely experienced. The uptime increases when systems perform without failure. That stability helps produce as earlier as possible, thus increasing satisfaction of the customers.
Water softening lowers the cost of detergent and chemicals. This reduces the cost of running in cleaning and processing. It also makes the facility environmentally friendly. A sewage water treatment plant helps manage residual water effectively, ensuring safe disposal and environmental compliance. Less frequent need for equipment replacement is associated with longer equipment life. Companies are able to save on long term capital expenditures. These savings go right into the pockets of increasing profits and the productivity of operations.
Maintenance Tips for Industrial Water Softeners to Ensure Efficiency
1. Conduct Regular Resin Bed Inspections- In time resin beads may foul or become inefficient. Have monthly inspections, replace media where necessary. This ensures uniform softening capacity, and flow rate.
2. Monitor Salt Levels in Brine Tanks- Maintain optimum levels of salt to promote good salt exchange. Refill with clean, high-quality salt. Note that avoid use of rock salt causing impurities.
3. Flush the System to Prevent Clogging- Sediment buildup is eliminated through normal backwashing. Stick to the schedule of the manufacturer to ensure no blockages of the flow occur and lack of pressure.
4. Track Water Hardness Post-Treatment- Hardness monitors shall be used to confirm performance. Unexpected spikes can mean either resin exhaustion or bypass problem.
5. Schedule Annual Professional Servicing- Hire certified technicians to check the entire system. They can detect hidden faults and readjust controls to the highest efficiency level.