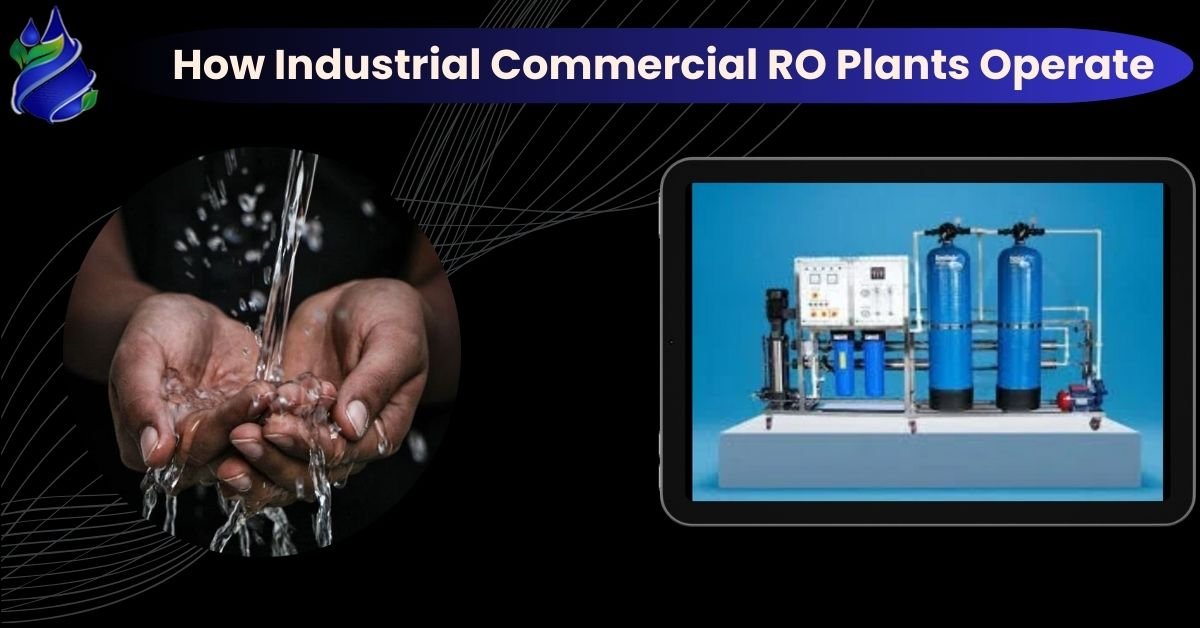
Introduction to Industrial Commercial RO Plants
Commercial industrial RO plants provide purified water for large-scale applications. These systems use a membrane to remove impurities, making water suitable for use in many industries. RO plants are found in the manufacturing, power generation, and food processing sectors. They help meet water quality standards for businesses and reduce environmental waste discharge risks. Reverse osmosis forces water through a semi-permeable membrane. It does that, separating the contaminants from the clean water. cThe RO plants not only enhance water quality but also cut operational costs by improving water recycling efficiency for industries.
The industrial RO plant has several important components which all work together to purify water. This system comprises a high-pressure pump, semi permeable membrane, and pretreatment filters. The high-pressure pump pushes water through the membrane and the filter removes large particle such as sediments or chlorine. Furthermore, a post treatment system can further refine water. The membrane is essential as it prevents salt, bacteria, and impurities from entering. The system is efficient only when all the parts work in coordination to deliver high quality water at scale.
Step-by-Step Process of Reverse Osmosis in Industrial Plants
Pretreatment of the water takes place where the water passes through filters to remove large particles. The high-pressure pump pushes the semi-permeable membrane with high pressure. It eliminates dissolved salts, bacteria and contaminants. The brine ejects and clean water flows towards the storage tank. Some RO plants recycle the brine for further purification. Monitoring system maintains the consistency in process. It is incredibly efficient, and operates automatically with minimal human input. This process is widely used because it produces high quality water at low operational cost.
Regular plant maintenance is must for best possible performance in industrial RO plant in India. Membranes, filters and pumps must be in good condition, which means plant operators must check the condition of them frequently. To prevent the system from clogging up with used oil and particles, technicians clean or replace filters regularly. Fouling of the membranes requires periodic cleaning, causing a loss of efficiency. Automated monitoring systems monitor important metrics such as pressure, water quality and allow for early detection of problems. Chemical dosing sometimes kills bacteria and scale (both biological and chemical) in the system. An efficient maintenance schedule extends plant life, minimizes downtime, and cuts operational costs.
Benefits of RO Systems in Industrial Applications
RO systems offer numerous benefits for industries that require high-quality water. They remove up to 99% of dissolved salts, bacteria, and organic materials, making them ideal for water purification. Cost savings are one of the biggest advantages. By using RO technology, industries can recycle water, reducing both water consumption and wastewater discharge. Additionally, RO systems require less energy compared to other water purification methods. They also ensure compliance with stringent environmental regulations by reducing pollutants. These systems are scalable and customizable, making them versatile for various industrial needs. Overall, RO technology is a sustainable and economical solution for water treatment.
Challenges Faced by Industrial RO Plants
Several challenges faced by the industrial RO Water plant hinder the plant’s efficiency and lifespan. Membrane fouling, where contaminants slow water flow in the membrane, is one of the major issues. One of the things that operators have to do to solve this, that is to clean or replace the membrane frequently. One of the major challenges in large scale operation is the high energy consumption.
- Although it is more energy efficient compared to other methods, it still consumes a significant amount of power. Another obstacle is chemical scaling, due to mineral deposits. Operators combat scaling by using anti-scalant chemicals and adjusting water chemistry. Biological fouling reduces the system performance as microorganisms grow on the membrane surface
- Regular monitoring and cleaning prevent this issue. The first challenge is to manage the brine or reject water that has the concentrated impurities in it. Brines still need to be safely and environmentally disposed of. All this compounds with strict environmental regulations on wastewater disposal. Nevertheless, RO plants are a key water supply in industrial applications. The operators continue to overcome these obstacles to ensure long-term efficiency.
Automation in Modern RO Plant Operations
1. Automation plays a fundamental role in modern RO plant performance and in minimizing the operational costs. Automated systems monitor real time critical parameters such as pressure, flow rate, and water quality. If the parameter is not at setpoint, the system corrects it, making sure that the performance stays constant.
2. Automation increases plant production efficiency by reducing manual intervention. RO systems are advanced software that integrates with RO systems and allows them to have remote access and control over operation.
3. Identifying problems and updating them allows operators to efficiently monitor system performance and respond promptly. Predictive maintenance also uses some automation.
4. Sensors detect early signs of wear and tear on membranes, filters, and pumps. With this, you can head problems off before they become an issue. In addition, automated chemical dosing system maintains the proper balance of anti-scalant and cleaners helping you to work efficiently. It reduces human error, allows a modern RO plant to be more productive by reducing downtime, and lowering operational and maintenance costs.
Conclusion
In conclusion, we present the advantages of industrial RO plant Manufacturers for large scale water purification. They remove impurities using advanced membranes and components to get high quality water for many industries. These systems undergo regular maintenance and automation to operate smoothly, consequently decreasing operational costs. Challenges such as membrane fouling, scaling and brine disposal have held back operators from further improvement in performance, but they have been able to overcome such challenges through innovation.
Future trends, including nanotechnology, renewable energy integration, as well as AI driven optimization, will further bind even greater efficiency. Industries that abide by environmental regulations can reduce freshwater consumption by implementing water recycling through industrial RO plant Supplier. Taken together, these systems have a key role in sustainable industrial water management