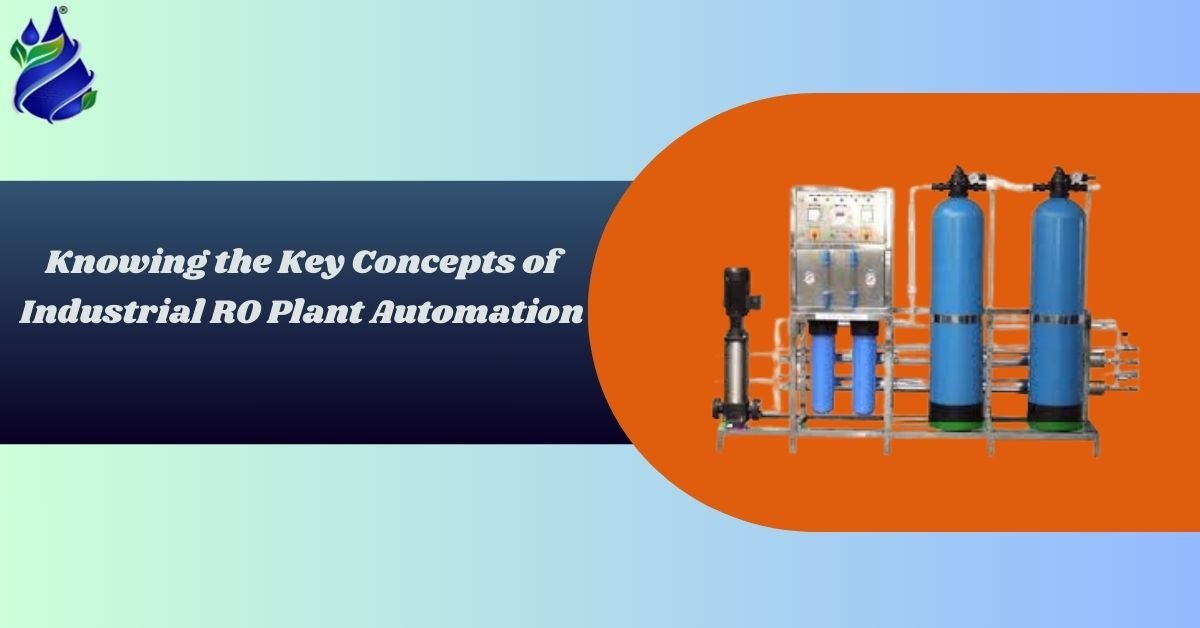
Understanding the Basics of Industrial RO Plant Automation
Reverse Osmosis system automation is also controlled and monitored with technology in Industrial RO plant automation. Water purification is better using automation and less human intervention. Various parameters are constantly monitored by sensors, programmable logic controllers (PLCs) for water pressure, flow rates, and pH levels. With this you are ensured of achieving optimal performance. Automated systems can adjust real-time operational settings to maintain water quality. Times of deviations from preset thresholds are notified automatically to operators, permitting instantaneous corrective action.
Also established are remote monitoring via cloud-based platforms which are further advanced. Automation helps to relieve human labour and enhances reliability and decrease the rate of human error. Filter cleaning, and chemical dosing, can also be automated. It reduces downtime, improves productivity. The system logs automatic data, making system optimization easier. In general, automation of the RO system results in better system efficiency and, hence, is an integral part of modern water treatment solutions.
Key Technologies Behind Industrial RO Plant Automation
Several key technologies support the automation of an industrial RO plant. Programmable logic controllers (PLCs) control system functions as the principal method. The sensors input data, the controllers process it, and activate predefined ways to change the system as needed. This is in the form of Human Machine Interfaces (HMIs), which provide visual feedback to operators, giving them insights to the real time system status.
Further critical are SCADA (Supervisory Control and Data Acquisition) systems for remote monitoring and control of operations. The system controls key parameters using flow meters and pressure sensors, which continuously measure them. Automated valves adjust water flow and pressure based on sensor feedback. With cloud-based monitoring solutions, operators are able to monitor system performance from anywhere. Combining these technologies, the RO plant operations become more efficient, reliable and scalable.
How Automation Enhances Efficiency in RO Water Treatment
Reverse Osmosis water treatment processes are very efficient using automation tremendously. The system automates water flow, pressure, and temperature regulation, optimizing them to ensure a good filtration process. The system achieves this in real time by preventing overload and saving energy.
It also automates membrane health to keep the membrane from fouling by cleaning and flushing on time. This is to extend the life span of costly RO membranes, and thus diminish the cost for operating. Swift troubleshooting is possible due to remote monitoring capabilities which helps in keeping system prone to downtime to minimize.
1. The system now automatically adds precise amounts, eliminating the possibility of overuse or wastage. Maintenance is automated and deemed the red flags facing potential issues before they become a problem. Using this predictive approach, resources are optimally utilized and the plant’s total environmental footprint is therefore minimized.
2. All industrial RO plants in India should ultimately be automated, and mastering key concepts is essential for success when automating an industrial RO plant. Understanding feedback loops is the first step. The loops allow the system to self-correct based on sensor input.
3. Therefore, next, it is important to know how to integrate programmable logic controllers (PLCs) with the sensors and actuators. Operators must understand Human Machine Interfaces, HMIs, which display the system data and are used for manual overrides when necessary. Another critical area is sensor calibration as inaccurate data will disrupt the whole system.
4. It is also important to fully understand system redundancy to prevent failure. Lastly, it is data analytics as analysing historical data can provide a better system optimization. These basic building blocks make sure that the system runs automatically without hiccups and runs smoothly.
Why Automation is Vital for Modern RO Systems
Automation is a necessary requirement in modern RO systems because it can assist in stream lining operations. This adds consistency to make sure water quality continues within parameters, without any manual intervention. Labor cost reduction comes from automated systems that allow for reduced use of human supervision. Finally, it also improves safety by virtually eliminating the chance for human to err.
Automation of water flow and chemical dosing is a necessity to ensure ideal membrane performance and achieve this, you need precision control. Lower operational costs and extended equipment life result. Moreover, it supports environmental sustainability by reducing energy consumption as well as by chemical waste. In general, the automation in modern RO systems plays a key role to make the overall process efficiency and reliability.
Boosting Water Purification Efficiency with RO Plant Automation
Development of RO Water plant automation improves water purification efficiency by a great extent. Automated systems monitor and adjust water quality by regulating flow rate and pressure for optimal conditions. The real time adjustments serve to maintain the RO membranes in top form, minimizing fouling, and maximize the water removal capability. By automating pumps to cycle their speeds based on water demand, automation also has the effect of reducing energy usage. Automated cleaning prevents scaling and biofouling, reducing downtime and maintenance needs. An operator can monitor performance and make adjustments from wherever it is that they happen to be located. Automation eliminates manual intervention, thereby maintaining the water quality with lower operational costs. In other words, automation will be a major factor to make Commercial RO systems run more efficiently and reliably.
Conclusion
- Finally, the automation of industrial RO plant is very important for water purification System. Automation has the capability of reducing manual oversight of the system and increased system efficiency by way of controlling key variables such as flow rates, pressure, and chemical dosing. RO membranes know that it is a must for them to perform optimally, minimize fouling and maximize shelf life. Real time adjustments are also possible with automation, thus maintaining a constant water quality.
- By utilizing PLCs, HMIs, and cloud systems, you can remotely monitor to proactively address issues without waiting for breakdowns. Plants’ automation of maintenance tasks including cleaning and flushing keeps downtime and operating costs down. Achieving reliability does not have to be costly, and it doesn’t have to involve high energy consumption, excessive chemical production and waste.
- Predictive analytics allows operators to optimize system performance and thus better manage resources. Industrial RO plant automation finally provides a smoother operation, better production water quality and, of course, long term cost savings, and that’s why it’s crucial part of modern water treatment solutions.